Introduction of Pipe and Tube
Pipe and tube are essential building materials that come in different sizes and shapes for various applications. However, many people use these terms interchangeably, even though they have different technical distinctions. Pipes are used for transport fluids and gases, while tubes are often used for structural purposes and utility applications. Understanding these technical differences is crucial to selecting the right material for your project. This article, packed with valuable information that will elevate your understanding of pipes and tubes in the construction industry. So, let’s dive in!
Common Applications for Pipe:
Pipes find extensive use in various industries due to their ability to transport fluids and gases efficiently. Some common applications include:
- Construction:
- Water Distribution:
- Industrial Processes:
- Oil and Gas Transport:
Common Applications for Tube:
Tubes, with their diverse shapes and sizes, find applications in a range of industries, including:
- Structural Engineering:
- Automotive Industry:
- Heat Exchangers:
- Aerospace
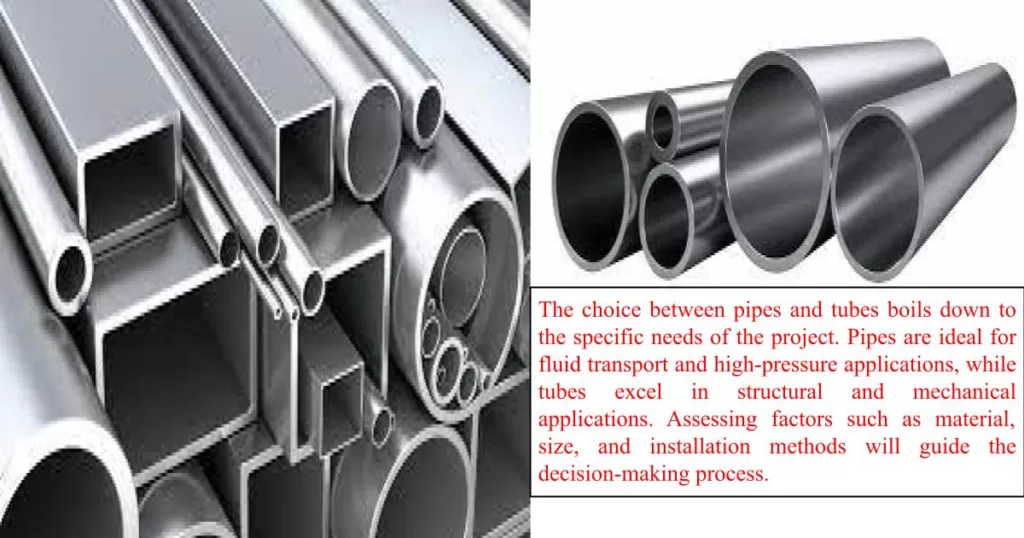
The Differences in Shape and Size
Pipe:
- Shape: Typically cylindrical with a round cross-section.
- Size: Designated by nominal pipe size (NPS) or diameter.
Tube:
- Shape: Can have various shapes, including round, square, or rectangular.
- Size: Specified by outside diameter (OD) and wall thickness.
Material Composition and Manufacturing Process
Pipe:
- Material Composition: Usually made from carbon steel, stainless steel, or other metals.
- Manufacturing Process: Often produced through seamless or welded methods.
Tube:
- Material Composition: Can be made from metals (steel, aluminum, copper) or non-metals (plastics, fiberglass).
- Manufacturing Process: Manufactured through processes like welding, seamless extrusion, or rotary piercing.
Understanding the Differences Between Pipe and Tube
Pipe:
- Primary Purpose: Designed for the conveyance of fluids, gases, or solids.
- Usage: Commonly used in plumbing, oil and gas transportation, and structural applications.
Tube:
- Primary Purpose: Used for structural applications, instrumentation, and the conveyance of fluids or gases.
- Usage: Widely applied in industries like construction, automotive, and aerospace.
Fluid Flow and Pressure Considerations
Pipe:
- Fluid Flow: Designed to accommodate the flow of large volumes of fluid or gas.
- Pressure Rating: Generally has a higher pressure rating than tubes.
Tube:
- Fluid Flow: Suited for applications where precise flow control is essential.
- Pressure Rating: Lower pressure rating compared to pipes.
Strength and Durability Comparisons
Pipe:
- Strength: Typically designed to withstand higher loads and pressures.
- Durability: Resistant to bending and deformation under heavy loads.
Tube:
- Strength: Generally lighter and may be less resistant to high pressures.
- Durability: Well-suited for applications where weight is a critical factor.
Standards and Specifications for Pipe and Tube
Standards and specifications are vital in ensuring the quality, safety, and compatibility of pipes and tubes in various applications. Different industries and regions may have specific standards that dictate the material composition, dimensions, and testing requirements. Adhering to these standards helps ensure that pipes and tubes meet the necessary criteria for structural integrity, performance, and regulatory compliance.
Maintenance and Care for Pipe and Tube
Proper maintenance and care are essential for the longevity and performance of pipes and tubes. This includes routine inspections, corrosion prevention measures, and adherence to recommended operating conditions. Understanding the environmental factors that may impact the materials, such as exposure to corrosive substances, is crucial for implementing effective maintenance strategies.
Definition and Characteristics of Tube
A tube is a hollow cylindrical structure with a specific set of characteristics that distinguish it from pipes. Unlike pipes, tubes are often defined by their outer diameter, thickness, and tolerance rather than nominal size. Tubes can be square, rectangular, or round and are commonly used in structural applications, where their versatility and strength make them suitable for various engineering and construction purposes.
Key Differences Between Pipe and Tube
Pipes and tubes are commonly used in various industries for fluid transport and structural applications. While they may seem similar, there are key differences between the two.
- Size and Dimensional Variations:
- Pipe: Generally, pipes have standardized sizes and are specified by their nominal pipe size (NPS) or DN (diameter nominal). They are designed to carry fluids and gases.
- Tube: Tubes come in a broader range of sizes, with more emphasis on the outside diameter (OD) and wall thickness. Tubes are often used for structural purposes.
- Shape and Structure:
- Pipe: Pipes are typically cylindrical and have a rigid structure. They are designed to withstand high pressure and are often used for conveying liquids and gases.
- Tube: Tubes can have various shapes, including round, square, and rectangular. They are more versatile and may be used for structural applications where flexibility is required.
- Usage and Application:
- Pipe: Pipes are primarily used for the transportation of fluids, such as water, oil, and gas. They are also commonly employed in plumbing and infrastructure projects.
- Tube: Tubes find applications in a broader range, including structural components in buildings, automotive frames, and engineering projects where strength and versatility are crucial.
Tube Characteristics and Applications
Tubes exhibit several characteristics that make them suitable for diverse applications:
- Versatility:
- Tubes come in various shapes and sizes, providing flexibility for different applications, including structural components, heat exchangers, and mechanical parts.
- Strength and Durability:
- Tubes are designed to withstand heavy loads and external pressures, making them ideal for applications where structural integrity is crucial.
- Corrosion Resistance:
- Many tubes are manufactured from corrosion-resistant materials, ensuring longevity and reliability, especially in harsh environments.
- Heat Transfer:
- Tubes are commonly used in heat exchangers, where they facilitate efficient heat transfer due to their relatively large surface area.
Manufacturing Processes for Pipe and Tube
- Pipe Manufacturing:
- Seamless Pipe: Produced without a welded seam, seamless pipes are created through extrusion or rotary piercing.
- Welded Pipe: Made by welding rolled steel sheets or strips, welded pipes are cost-effective and suitable for various applications.
- Tube Manufacturing:
- Hot Extrusion: Tubes are formed by forcing heated metal through a die.
- Cold Drawing: Tube production involves pulling the material through a die at room temperature, resulting in a smooth finish.
Installation and Compatibility Considerations
Efficient installation and compatibility are paramount in any piping or tubing system. Installation considerations encompass factors such as welding, threading, and joining methods. Compatibility involves understanding the materials used in pipes and tubes, as well as their resistance to corrosion and other environmental factors. Proper installation practices and material compatibility contribute to the longevity and reliability of the system.
Factors to Consider When Choosing Between Pipe and Tube
Choosing between pipes and tubes depends on various factors, including the intended application, pressure requirements, and structural considerations. Pipes are generally designed for conveying fluids under pressure, while tubes find application in structural and mechanical contexts. Considerations such as cost, ease of installation, and specific performance requirements play a pivotal role in determining whether a pipe or tube is more suitable for a given task.
Conclusion: Which is Better for Your Needs?
Ultimately, the choice between pipes and tubes boils down to the specific needs of the project. Pipes are ideal for fluid transport and high-pressure applications, while tubes excel in structural and mechanical applications. Assessing factors such as material, size, and installation methods will guide the decision-making process. By carefully considering these factors, one can determine whether pipes or tubes better align with the requirements of the project, ensuring optimal performance and longevity.