Complete Guide to Rotary Vacuum Dryer (RVD) Design, Construction, and Sizing
Rotary Vacuum Dryers (RVDs) are indispensable in industries such as pharmaceuticals, chemicals, food, and specialty materials for drying heat-sensitive products under vacuum. Their ability to operate at low temperatures while removing moisture efficiently makes them ideal for high-value and sensitive compounds. In this comprehensive guide, we’ll walk through the fundamentals of RVD design, construction, and sizing—equipping both beginners and seasoned professionals with the knowledge needed for process optimization and equipment selection.
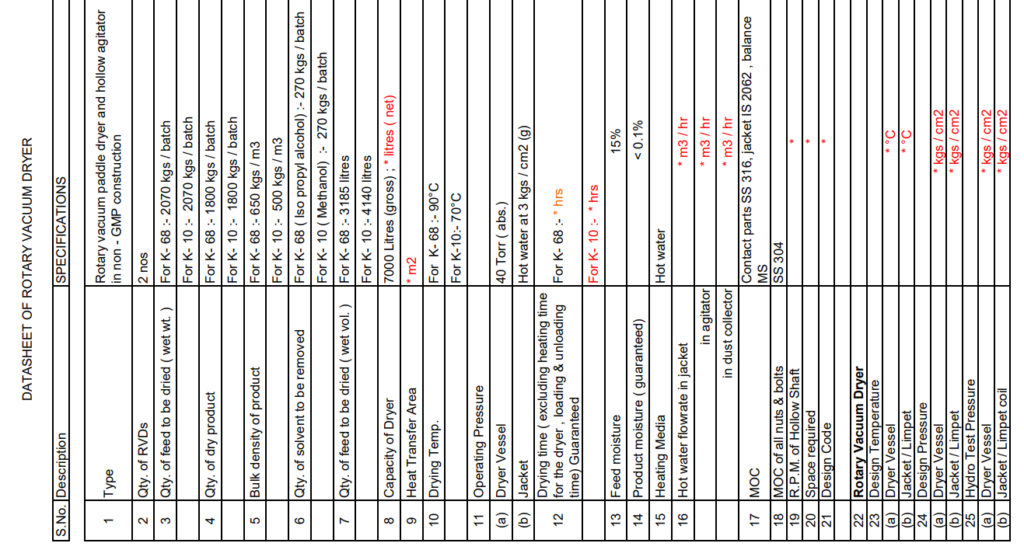
What is a Rotary Vacuum Dryer (RVD)?
A Rotary Vacuum Dryer is a horizontal cylindrical jacketed vessel with a central agitator. The dryer is operated under vacuum to reduce the boiling point of solvents, which enhances drying efficiency for thermolabile substances.
Key Benefits of RVDs:
- Efficient drying of heat-sensitive materials
- Low solvent boiling points under vacuum
- Better control over moisture content
- Energy-saving through reduced drying temperatures
- Closed operation minimizes contamination and solvent losses
Applications of Rotary Vacuum Dryers
RVDs are extensively used across multiple industries:
- Pharmaceuticals: For drying Active Pharmaceutical Ingredients (APIs) and intermediates
- Chemical Industry: For drying specialty and fine chemicals
- Food Industry: For preserving sensitive ingredients like flavoring agents
- Agrochemicals: For pesticide and herbicide production
💡 For a deeper dive into heat transfer principles involved in dryers, check out our post on Types of Heat Exchangers with engineering illustrations.
Construction of a Rotary Vacuum Dryer
An RVD consists of several critical components designed for robustness and reliability. Here’s a breakdown:
- Cylindrical Vessel The main chamber is a horizontal cylindrical shell made from SS316 or carbon steel. It is typically jacketed to allow circulation of hot water, steam, or thermal oil.
- Agitator and Shaft The central agitator facilitates uniform drying by mixing the material. It is equipped with blades or paddles designed to minimize dead zones and ensure even heat distribution.
- Drive Assembly The agitator is rotated via a motor and gearbox, often fitted with a variable frequency drive (VFD) for speed control.
- Vacuum System A vacuum pump removes vapors and lowers the pressure inside the dryer, allowing drying at reduced temperatures.
- Dust Filter and Condenser A condenser system recovers solvents while a dust collector ensures particulates are not drawn into the vacuum pump.
- Discharge Valve At the end of the cycle, the product is discharged through a bottom or side-mounted valve.
Step-by-Step Guide to RVD Design
Designing an RVD involves multiple steps focused on thermal performance, mechanical strength, and drying efficiency. Here’s a systematic guide:
Step 1: Define Process Parameters Before sizing the RVD, collect all essential process data:
Parameter | Description |
---|---|
Material | Type and nature (organic/inorganic) |
Initial & Final Moisture (%) | Wet basis or dry basis |
Batch Size | In kg or liters per batch |
Solvent Type & Quantity | Water, alcohol, etc. |
Operating Pressure | Vacuum range (mmHg or mbar) |
Operating Temperature | Jacket temperature (°C) |
- Download a prefilled RVD Process Data Sheet Spreadsheet to structure this input efficiently.
- Step 2: Material and Thermal Balance
- Estimate the heat required to evaporate the solvent:
- Q=m×λQ = m \times \lambda
- Where:
- QQ = Heat required (kJ)
- mm = Mass of solvent to be removed (kg)
- λ\lambda = Latent heat of vaporization (kJ/kg)
- Add sensible heat if initial material is at lower temperature.
- For automatic calculations, use our Dryer Energy Calculation Sheet.
- Step 3: Surface Area Estimation
- Drying is governed by the heat transfer from the jacket to the material. Required surface area is:
- A=QU×ΔT×tA = \frac{Q}{U \times \Delta T \times t}
- Where:
- AA = Required heat transfer area (m²)
- UU = Overall heat transfer coefficient (W/m²·K)
- ΔT\Delta T = Temperature difference between jacket and material
- tt = Drying time (s)
- Step 4: Agitator and RPM Selection
- Low RPM (3–10 rpm) is standard for gentle mixing. The agitator’s design should accommodate:
- Viscosity of the slurry
- Fragility of crystals
- Required shear
- Blade geometry can be paddle, anchor, or helical ribbon depending on process demands.
- RVD Sizing: A Practical Example
Let’s take an example of drying 100 kg of wet cake with 30% moisture (w.b.) to 1% final moisture.
- Solvent: Water
- Latent heat: 2257 kJ/kg
- Jacket temperature: 90°C
- Product initial temperature: 30°C
- Time allowed: 2 hours
Step-by-Step Sizing Summary:
- Moisture Removed: = 30 kg – 1 kg = 29 kg
- Energy Required: = 29 × 2257 = 65,453 kJ
- Required Surface Area: Assuming U = 300 W/m²·K, ΔT = 60°C,
- A=65,453300×60×7200≈0.5 m²A = \frac{65,453}{300 \times 60 \times 7200} \approx 0.5 \text{ m²}
- Volume Considerations: Dryer should accommodate ~120–150% of product volume for proper mixing.
Vacuum Rating:
Designed for ~50–100 mmHg absolute pressure
- Use this RVD Sizing Excel Tool to streamline such calculations for various capacities.
Design Considerations for RVD
1. Vacuum Integrity All seals, gaskets, and joints must withstand vacuum without leakage. Consider mechanical seals and vacuum-rated sight glasses.
2. Cleaning and GMP Compliance In the pharmaceutical and food industry, RVDs must support CIP (Clean-in-Place) systems and polished internal finishes.
3. Heat Transfer Jacket Options include:
- Steam Jacket
- Hot Water Jacket
- Thermic Fluid Circulation
- Select based on temperature range and thermal control needs.
4. Drive System Inert atmosphere or flameproof motors are necessary in hazardous area classifications (ATEX/IECEx zones).
Spreadsheet Tools for Rotary Vacuum Dryer Design
👉 Explore our ready-to-use Rotary Dryer Design Spreadsheets covering:
- Heat Load Calculations
- Vacuum Sizing Requirements
- Jacket Area Estimation
- Drying Time Estimation
- Moisture Balance Charts
These tools are essential for mechanical design engineers, project consultants, and plant managers looking to save time and improve accuracy.
Troubleshooting Common Issues in RVDs
Issue | Cause | Solution |
---|---|---|
Incomplete Drying | Inadequate jacket temperature | Increase jacket set point or time |
Vacuum Leakage | Worn-out gaskets or seals | Replace or re-torque connections |
Material Buildup | Improper agitator blade design | Use self-cleaning or Teflon-coated blades |
Motor Overload | Overfilled material or high torque | Reduce batch size or use gear reducer |
For more practical troubleshooting guidance, refer to our Maintenance Tools Section.
Comparison: RVD vs Other Dryers
Parameter | RVD | Tray Dryer | Fluid Bed Dryer |
---|---|---|---|
Heat Sensitivity | Excellent | Moderate | Poor |
Vacuum Operation | Yes | No | Optional |
Drying Time | 2–4 hrs | 6–12 hrs | 0.5–2 hrs |
Agitation/Mixing | Yes (gentle) | No | Yes (turbulent) |
Capital Cost | Medium to High | Low | Medium |
Conclusion: Why Choose RVD?
A Rotary Vacuum Dryer is a versatile and efficient solution for drying moisture-sensitive or heat-sensitive materials under controlled vacuum and temperature conditions. Proper sizing and design ensure long equipment life, energy efficiency, and product consistency. Whether you’re upgrading existing systems or commissioning new units, applying fundamental engineering principles can lead to better process outcomes.
To simplify your engineering workflow, download our expert-curated Drying Equipment Spreadsheets and explore in-depth articles on GrowMechanical.com to stay ahead in your field.
Related Resources: