What is a Butterfly Valve and How Does it Work?
A butterfly valve is a type of valve used to control the flow of a fluid in a pipeline. It is called a butterfly valve because of its shape, which resembles that of a butterfly. The valve consists of a disc that rotates around a shaft located at the center of the valve body. When the disc is in the open position, the fluid can flow freely through the valve. When the disc is in the closed position, the fluid flow is blocked.
They are popular because of their compact design, low cost, and ease of use. Butterfly valves can be operated manually, pneumatically, or electrically, depending on the application.
One of the main advantages of butterfly valves is their low pressure drop, which means that they do not significantly restrict the flow of fluid through the pipeline. This makes them an ideal choice for applications where a high flow rate is required. Another advantage is their quick opening and closing time, which makes them useful for processes that require frequent flow adjustments.
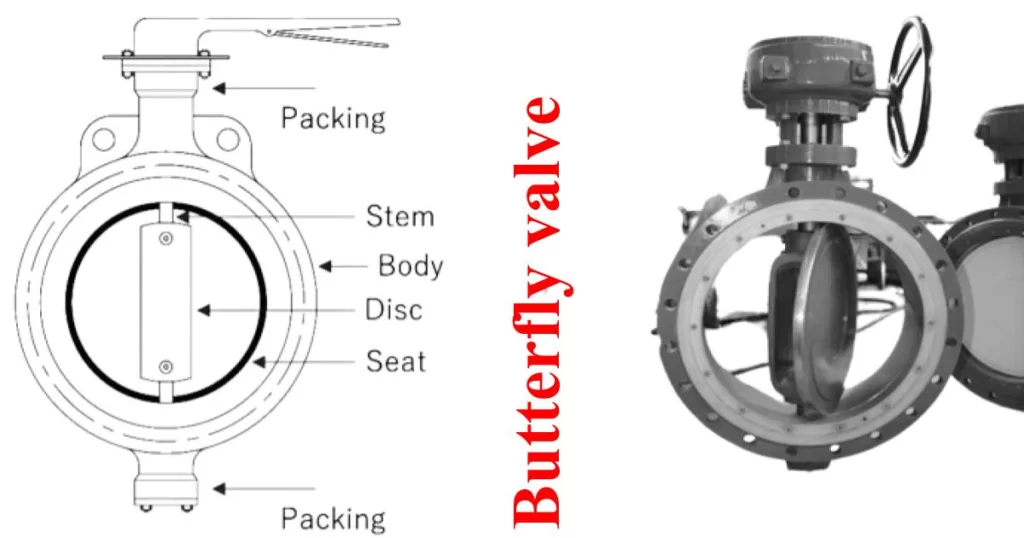
A Comprehensive Guide to Types and Applications of Butterfly valve
Butterfly valves are available in different types, each designed for specific applications. Here are some of the most common types of butterfly valves and their uses:
- Wafer Butterfly Valve – A wafer butterfly valve is a type of butterfly valve that is designed to fit between two flanges in a pipeline. This type of valve is ideal for applications that require a low-profile valve that can be easily installed and removed. Wafer butterfly valves are commonly used in HVAC, water treatment, and chemical processing applications.
- Lug Butterfly Valve – A lug butterfly valve is a type of butterfly valve that has threaded inserts in the valve body. These inserts allow the valve to be bolted directly to the pipeline, without the need for flanges. Lug butterfly valves are commonly used in applications where frequent disassembly is required, such as in pipelines that require maintenance or repair.
- Double Offset Butterfly Valve – A double offset butterfly valve is a type of butterfly valve that has a disc that is offset from the center of the valve body. This design reduces the amount of friction between the disc and the valve seat, which makes the valve more durable and longer-lasting. Double offset butterfly valves are commonly used in applications that require high durability and low maintenance, such as in the oil and gas industry.
- Triple Offset Butterfly Valve – A triple offset butterfly valve is a type of butterfly valve that has a disc that is offset from the center of the valve body in three different directions. This design reduces the amount of friction between the disc and the valve seat even further, which makes the valve even more durable and longer-lasting than a double offset butterfly valve. Triple offset butterfly valves are commonly used in applications that require high performance and reliability, such as in the chemical and petrochemical industries.
Choosing the Perfect Butterfly Valve: A Step-by-Step Guide to Selection and Sizing
Selecting the right butterfly valve for your application is essential to ensure optimal performance and reliability. Here are some factors to consider when selecting a butterfly valve:
- Operating Conditions – Consider the operating conditions of your application, such as the temperature and pressure of the fluid being transported, the flow rate, and the type of fluid being transported. Make sure the valve you select can handle the operating conditions of your application.
- Material Selection – Choose a butterfly valve made from the appropriate material for your application. Factors to consider include the temperature and pressure of the fluid being transported, the corrosiveness of the environment, and the required strength and durability of the valve.
- Valve Type – Consider the different types of butterfly valves available, such as wafer, lug, double offset, and triple offset butterfly valves. Choose the type of valve that best meets the specific needs of your application.
- Valve Size – Select a valve size that matches the size of your pipeline. A valve that is too small or too large for your pipeline can result in performance issues and may cause damage to the valve and the pipeline.
- End Connections – Choose the appropriate end connections for your application. Butterfly valves can be equipped with different types of end connections, such as flanged, threaded, or grooved connections.
- Operational Requirements – Consider the operational requirements of your application, such as the frequency of use, the need for manual or automatic operation, and the type of actuator required for automatic operation.
- Compliance with Standards
- Ensure that the butterfly valve you select meets applicable industry standards, such as ANSI, API, or ISO standards.
Mastering butterfly Valve Selection: Understanding Properties, Standards, and Metrology for Optimal Performance
When selecting a butterfly valve, it’s important to consider the following properties:
- Flow Coefficient (Cv) – The flow coefficient is a measure of the valve’s ability to regulate fluid flow. It is defined as the flow rate of water in gallons per minute (GPM) that passes through the valve at a pressure drop of one pound per square inch (PSI). A higher Cv indicates a valve with greater flow capacity.
- Example: A butterfly valve with a Cv of 200 can handle a flow rate of 200 GPM with a pressure drop of 1 PSI.
- Pressure Rating – The pressure rating indicates the maximum pressure at which the valve can operate safely. It is typically expressed in pounds per square inch (PSI).
- Example: A butterfly valve with a pressure rating of 150 PSI can operate safely at a maximum pressure of 150 PSI.
- Temperature Rating- The temperature rating indicates the maximum temperature at which the valve can operate safely. It is typically expressed in degrees Fahrenheit (°F) or Celsius (°C).
- Example: A butterfly valve with a temperature rating of 250°F can operate safely at a maximum temperature of 250°F.
- Material of Construction – The material of construction determines the valve’s resistance to corrosion, abrasion, and wear. Common materials include cast iron, stainless steel, and carbon steel.
- Example: A butterfly valve made of stainless steel provides superior corrosion resistance compared to a cast iron valve.
- Codes and Standards: Various codes and standards are used to ensure the quality and reliability of butterfly valves. Here are a few examples:
- API 609: This standard specifies design, testing, and performance requirements for resilient-seated butterfly valves used in oil and gas industry applications.
- MSS SP-67: This standard specifies requirements for butterfly valves with flanged or butt-welding ends used in industrial applications.
- ASME B16.34: This standard specifies requirements for valve design, testing, and performance in a variety of industrial applications.
Metrology and testing of Butterfly valve
Metrology is the science of measurement, and it plays an essential role in ensuring the accuracy and precision of butterfly valves. Here are some important aspects of metrology in relation to butterfly valves:
- Measurement Accuracy – Butterfly valves must be designed and manufactured to precise specifications to ensure optimal performance. Metrology plays a critical role in measuring and verifying the accuracy of various aspects of the valve, such as the size and shape of the valve body, the dimensions of the disc and stem, and the tolerances of the valve components.
- Calibration – Calibration is the process of verifying the accuracy of measuring equipment and ensuring that it is traceable to a recognized standard. Calibration of measuring devices such as micrometers, gauges, and flow meters is essential to ensure the accuracy of measurements taken during the manufacturing and testing of butterfly valves.
- Quality Control – Quality control is the process of monitoring and verifying that a product meets the required quality standards. Metrology is an important aspect of quality control in butterfly valve manufacturing, as it allows manufacturers to verify that the valves meet the required specifications and performance standards.
- Non-Destructive Testing – Non-destructive testing is a metrological technique used to test the integrity of materials and structures without causing damage to the sample being tested. This technique is often used in the testing of butterfly valves to detect defects and ensure the reliability and safety of the valve.
- Industry Standards – There are several industry standards and codes that govern the metrology requirements for butterfly valves. For example, API 609 specifies the requirements for the design, manufacture, and testing of butterfly valves used in the oil and gas industry.
Tailoring Butterfly Valve Solutions: Meeting Specific Requirements for Diverse Industrial Applications
Butterfly valves are used in a wide range of applications, and specific requirements may vary depending on the intended use of the valve. Here are some common requirements for butterfly valve uses in various industries:
- Oil and Gas Industry – Butterfly valves used in the oil and gas industry must be designed and manufactured to withstand harsh environments and high-pressure applications. They should also be able to handle a wide range of temperatures and corrosive fluids.
- Water Treatment Industry – Butterfly valves used in water treatment applications must be resistant to corrosion and erosion caused by chemicals and water flow. They should also be designed to prevent water hammer and maintain a tight seal to prevent leakage.
- HVAC Industry – Butterfly valves used in heating, ventilation, and air conditioning (HVAC) systems must be able to regulate the flow of air or water in the system. They should also be designed to operate quietly and efficiently.
- Food and Beverage Industry – Butterfly valves used in the food and beverage industry must be designed and manufactured to meet strict sanitary standards. They should be easy to clean and sanitize, and should not contaminate the food or beverage product.
- Pharmaceutical Industry – Butterfly valves used in the pharmaceutical industry must be designed and manufactured to meet stringent regulatory requirements. They should be easy to clean and sanitize, and should not contribute to contamination of the product.
- Chemical Industry – Butterfly valves used in the chemical industry must be resistant to corrosion and able to handle a wide range of chemical substances. They should also be designed to prevent leakage and minimize the risk of chemical spills.
Right-Sizing butterfly Valves for Optimal Pipeline Performance: Calculating Size and Type with Formulas and Examples
Butterfly valves are commonly used in pipelines to regulate the flow of fluids. Selecting the appropriate valve size and type is critical to ensuring optimal performance and efficiency of the pipeline system. Here is an in-depth guide to calculating butterfly valve size and types for pipelines:
Calculate the Flow Rate – The first step in selecting the appropriate butterfly valve size is to calculate the flow rate of the fluid in the pipeline. This can be calculated using the following formula: Q = A x V
Where: Q = flow rate (m3/h) A = cross-sectional area of the pipeline (m2) V = velocity of fluid in the pipeline (m/s)
Determine the Required Valve Size – Once the flow rate has been calculated, the next step is to determine the required valve size. This can be done by using the following formula: D = √(4Q/πv)
Where: D = diameter of the valve (m) Q = flow rate (m3/h) v = velocity of the fluid in the valve (m/s)
Select the Type of Butterfly Valve
There are two types of butterfly valves commonly used in pipelines: wafer type and lug type. The choice between the two depends on the specific requirements of the pipeline system. Here is a brief overview of each type:
- Wafer Type: Wafer type butterfly valves are designed to fit between two flanges and are held in place by bolts. They are compact, lightweight, and easy to install. They are ideal for pipelines with limited space.
- Lug Type: Lug type butterfly valves have threaded inserts on both sides of the valve body that allow them to be bolted into the pipeline. They are suitable for use in high-pressure applications and are often used in larger pipeline systems.
Determine the Pressure Rating
The pressure rating of the butterfly valve should be selected based on the maximum pressure expected in the pipeline system. The pressure rating of the valve should be higher than the maximum pressure in the system to ensure safe and reliable operation.
Code and Standards for butterfly Valve Parts: A Guide to Ensuring Quality and Reliability in Selection
When selecting a butterfly valve, it’s important to consider the different parts and their codes and standards to ensure optimal performance and reliability. Here is a list of the different parts of a butterfly valve and their codes and standards:
- Body – The body of the butterfly valve is the main component that houses the disc and stem. The body must be designed and manufactured to withstand the pressure and temperature of the fluid in the pipeline. Common codes and standards for butterfly valve bodies include ANSI B16.34 and API 609.
- Disc – The disc is the component of the butterfly valve that regulates the flow of fluid. The disc can be either a flat plate or a curved plate. The disc must be designed and manufactured to provide a tight seal and prevent leakage. Common codes and standards for butterfly valve discs include API 609 and ASME B16.34.
- Stem – The stem of the butterfly valve connects the disc to the actuator. The stem must be designed and manufactured to withstand the torque required to operate the valve. Common codes and standards for butterfly valve stems include API 609 and ASME B16.34.
- Seat – The seat of the butterfly valve is the component that provides a tight seal between the disc and the body. The seat must be designed and manufactured to withstand the pressure and temperature of the fluid in the pipeline. Common codes and standards for butterfly valve seats include API 609 and ASME B16.34.
- Actuator – The actuator of the butterfly valve is the component that controls the position of the disc. The actuator can be either manual or automatic, and must be designed and manufactured to provide accurate and reliable control. Common codes and standards for butterfly valve actuators include API 609 and ASME B16.34.
Prevent Leaks with Our Comprehensive Leakage Class for All Types of Valves
Leakage class is an important factor to consider when selecting a valve for a particular application. It refers to the amount of leakage that is allowed through the valve in its closed position. The different types of leakage class for valves are as follows:
- Class I leakage is the lowest level of leakage allowed through a valve in its closed position. It is commonly used in applications where leakage cannot be tolerated, such as in hazardous or toxic environments.
- Class II leakage is a slightly higher level of leakage allowed through a valve in its closed position. It is commonly used in applications where a small amount of leakage can be tolerated, such as in non-hazardous environments.
- Class III leakage is the highest level of leakage allowed through a valve in its closed position. It is commonly used in applications where leakage is not critical, such as in water treatment plants or irrigation systems.
It’s important to note that the leakage class can vary depending on the type of valve. Here are the different types of valves and their corresponding leakage classes:
- Gate Valves – Class I Leakage: Zero leakage is allowed through the valve in its closed position.
- Globe Valves – Class I Leakage: Zero leakage is allowed through the valve in its closed position.
- Ball Valves – Class I Leakage: Zero leakage is allowed through the valve in its closed position.
- Butterfly Valves – Class I Leakage: Zero leakage is allowed through the valve in its closed position.
- Check Valves – Class I Leakage: Zero leakage is allowed through the valve in its closed position.
DOWNLOAD YOUR Ball BUTTERFLY VALVE TYEPS SELECTION APPLICATION PDF HERE – CLICK ON TEXT
Maximizing Efficiency: How to Calculate Pressure Drop in butterfly Valves for Optimal Performance
Calculating pressure drop is an important consideration when selecting a butterfly valve for a particular application. Pressure drop refers to the difference in pressure between the inlet and outlet of the valve. Here’s how to calculate pressure drop for a butterfly valve:
- Determine the flow rate of the fluid through the valve, measured in cubic meters per hour (m³/h).
- Determine the viscosity of the fluid, measured in centipoise (cP). This value can be found in the fluid’s technical data sheet.
- Determine the density of the fluid, measured in kilograms per cubic meter (kg/m³). This value can also be found in the fluid’s technical data sheet.
- Determine the valve’s Cv value, which is a measure of the valve’s flow capacity. This value can be found in the manufacturer’s data sheet for the valve.
Use the following formula to calculate the pressure drop:
Pressure drop (ΔP) = [Cv x (Flow rate / (Density x Specific gravity))]²
Where: Cv is the valve’s flow coefficient
Flow rate is the volume of fluid passing through the valve per unit of time
Density is the mass per unit volume of the fluid
Specific gravity is the ratio of the density of the fluid to the density of water at a specified temperature
By calculating the pressure drop for a butterfly valve, you can ensure that the valve is selected correctly for the application and will operate within the desired pressure range.
Gate Valve vs Butterfly Valve: Which is the Better Choice for Your Application
Butterfly valves and gate valves are two common types of valves used in industrial applications. While they both control the flow of fluids, they have some key differences that make each more suitable for certain applications. Here’s a comparison of butterfly valve vs gate valve:
- Design – Butterfly valves have a disc that rotates around a shaft to control the flow of fluid, while gate valves have a gate or wedge that moves up and down to open or close the valve.
- Size and Weight – Butterfly valves are typically smaller and lighter than gate valves, which makes them more suitable for applications with limited space or weight restrictions.
- Flow Control – Butterfly valves can be used for both on/off and throttling applications, while gate valves are typically used only for on/off applications.
- Pressure Drop – Gate valves have a lower pressure drop than butterfly valves, which means they are more suitable for applications where pressure drop is a concern.
- Leakage – Gate valves typically have a better seal than butterfly valves, which makes them more suitable for applications where leakage cannot be tolerated.
- Maintenance – Butterfly valves are generally easier to maintain and repair than gate valves, as they have fewer parts and are easier to access.
Butterfly Valve vs Ball Valve: Which is the Right Choice for Your Flow Control Needs?
- Design – Butterfly valves have a rotating disc that controls the flow of fluid, while ball valves have a sphere-shaped disc that rotates to control the flow of fluid.
- Size and Weight – Butterfly valves are typically smaller and lighter than ball valves, which makes them more suitable for applications with limited space or weight restrictions.
- Flow Control – Butterfly valves can be used for both on/off and throttling applications, while ball valves are typically used only for on/off applications.
- Pressure Drop – Butterfly valves have a higher pressure drop than ball valves, which means they are less suitable for applications where pressure drop is a concern.
- Leakage – Ball valves typically have a better seal than butterfly valves, which makes them more suitable for applications where leakage cannot be tolerated.
- Maintenance – Butterfly valves are generally easier to maintain and repair than ball valves, as they have fewer parts and are easier to access.
Ensuring Proper Installation: A Comprehensive Checklist for butterfly Valve Installation
Installing a butterfly valve is an important task that requires attention to detail to ensure proper functioning and prevent issues down the line. Here’s a checklist to follow for butterfly valve installation:
- Check Valve and Components – Ensure that the valve and all its components are in good condition and match the specifications required for the installation.
- Prepare the Installation Site – Ensure that the installation site is clean, dry, and free of debris that may interfere with the installation.
- Align the Valve – Ensure that the valve is properly aligned with the piping system and that the flanges are lined up correctly.
- Tighten Flange Bolts – Tighten the flange bolts to the correct torque specified in the installation manual.
- Check Alignment Again – Check the alignment of the valve once again to ensure that it is properly aligned with the piping system.
- Lubricate – Lubricate the valve stem and ensure that the valve opens and closes smoothly.
- Connect Actuator – If the valve has an actuator, connect it according to the manufacturer’s instructions.
- Test the Valve – Perform a pressure test to ensure that the valve is functioning properly and that there are no leaks.
- Inspect the Installation – Inspect the installation to ensure that all components are properly installed and tightened.
- Record the Installation – Record the installation details and the valve’s position for future reference.
By following this checklist, you can ensure a proper butterfly valve installation that will function efficiently and effectively for years to come.
Ensure Optimal Performance: A Comprehensive butterfly Valve Inspection Checklist
Inspection is an important part of maintaining the efficient and effective functioning of a butterfly valve. Here’s a checklist to follow for butterfly valve inspection:
- Check Valve Body and Components – Inspect the valve body and all its components for any signs of wear, corrosion, or damage.
- Check Seat and Seal – Inspect the seat and seal of the valve for any signs of wear or damage. Check for proper tightness and sealing.
- Check Disc – Inspect the disc of the valve for any signs of damage or warping that could affect the valve’s function.
- Check Stem – Inspect the valve stem for any signs of wear, corrosion, or damage.
- Check Actuator – If the valve has an actuator, inspect it for proper functioning and any signs of wear or damage.
- Lubricate – Lubricate the valve stem and ensure that the valve opens and closes smoothly.
- Perform Pressure Test – Perform a pressure test to ensure that the valve is functioning properly and that there are no leaks.
- Inspect the Installation – Inspect the installation to ensure that all components are properly installed and tightened.
- Record Inspection Results – Record the inspection results and make note of any issues that need to be addressed.
By following this checklist, you can ensure that your butterfly valve is properly inspected and maintained, which will help to prevent issues and ensure optimal functioning over time.
Troubleshooting butterfly Valve Failures: Identifying Causes and Solutions for Optimal Performance
Butterfly valves are reliable and efficient components, but they can still experience failures or issues that can affect their functioning. Here are some common failure causes and troubleshooting techniques for butterfly valves:
- Leakage – Failure Cause: Worn or damaged seat, seal or disc
- Troubleshooting: Replace or repair damaged components, check and adjust valve torque.
- Low Flow Capacity – Failure Cause: Wrong valve size, high pressure drop
- Troubleshooting: Check valve size, verify that the valve is correctly sized for the application, check pressure drop.
- High Torque –Failure Cause: Friction, high operating temperature
- Troubleshooting: Lubricate the valve, adjust or replace valve components, check valve operating temperature.
- Valve Stuck or Difficult to Operate – Failure Cause: Dirt, debris or rust accumulation
- Troubleshooting: Clean or replace valve components, lubricate the valve, check for damage or wear on valve components.
- Actuator Failure – Failure Cause: Electrical, mechanical or pneumatic problems
- Troubleshooting: Inspect and test the actuator, replace any damaged or worn components, check electrical connections, and pneumatic lines.
- Corrosion –Failure Cause: Exposure to corrosive materials
- Troubleshooting: Replace corroded components, adjust the valve to prevent further corrosion.
- Noise or Vibration – Failure Cause: Unbalanced disc, improper installation
- Troubleshooting: Check valve installation, adjust the valve to ensure proper balance.
By addressing these common failure causes and performing the recommended troubleshooting techniques, you can keep your butterfly valve functioning smoothly and efficiently. Regular maintenance and inspections are also key to preventing issues and ensuring optimal valve performance.
Selecting the Right Material: A Comprehensive Guide to butterfly Valve Material Specifications and Grades
Butterfly valves are made from a variety of materials to suit different applications and operating conditions. Here are some common materials specifications and grades for butterfly valve components:
- Valve Body – Materials: Carbon steel, stainless steel, cast iron, ductile iron
- Grades: ASTM A216 WCB, ASTM A351 CF8M, ASTM A536 65-45-12, ASTM A395 60-40-18
- Valve Disc – Materials: Stainless steel, carbon steel, ductile iron, aluminum bronze
- Grades: ASTM A351 CF8M, ASTM A216 WCB, ASTM A536 65-45-12, ASTM B148 C95800
- Valve Seat – Materials: EPDM, Buna-N, PTFE, Viton, Neoprene, silicone
- Grades: ASTM D2000, ASTM D1418
- Valve Stem – Materials: Stainless steel, carbon steel, monel, hastelloy
- Grades: ASTM A276, ASTM A564, ASTM B164
- Valve Seal – Materials: PTFE, EPDM, Viton, Buna-N, silicone
- Grades: ASTM D2000, ASTM D1418
- Valve Bolts and Nuts – Materials: Carbon steel, stainless steel
- Grades: ASTM A193 B7, ASTM A320 L7, ASTM A194 2H, ASTM A194 8
Note that the specific materials and grades used in a butterfly valve will depend on the application and operating conditions. It is important to consult with a valve manufacturer or supplier to ensure that the valve is made from the appropriate materials for the intended use.